The Importance of a Central Lubrication System for Your Business
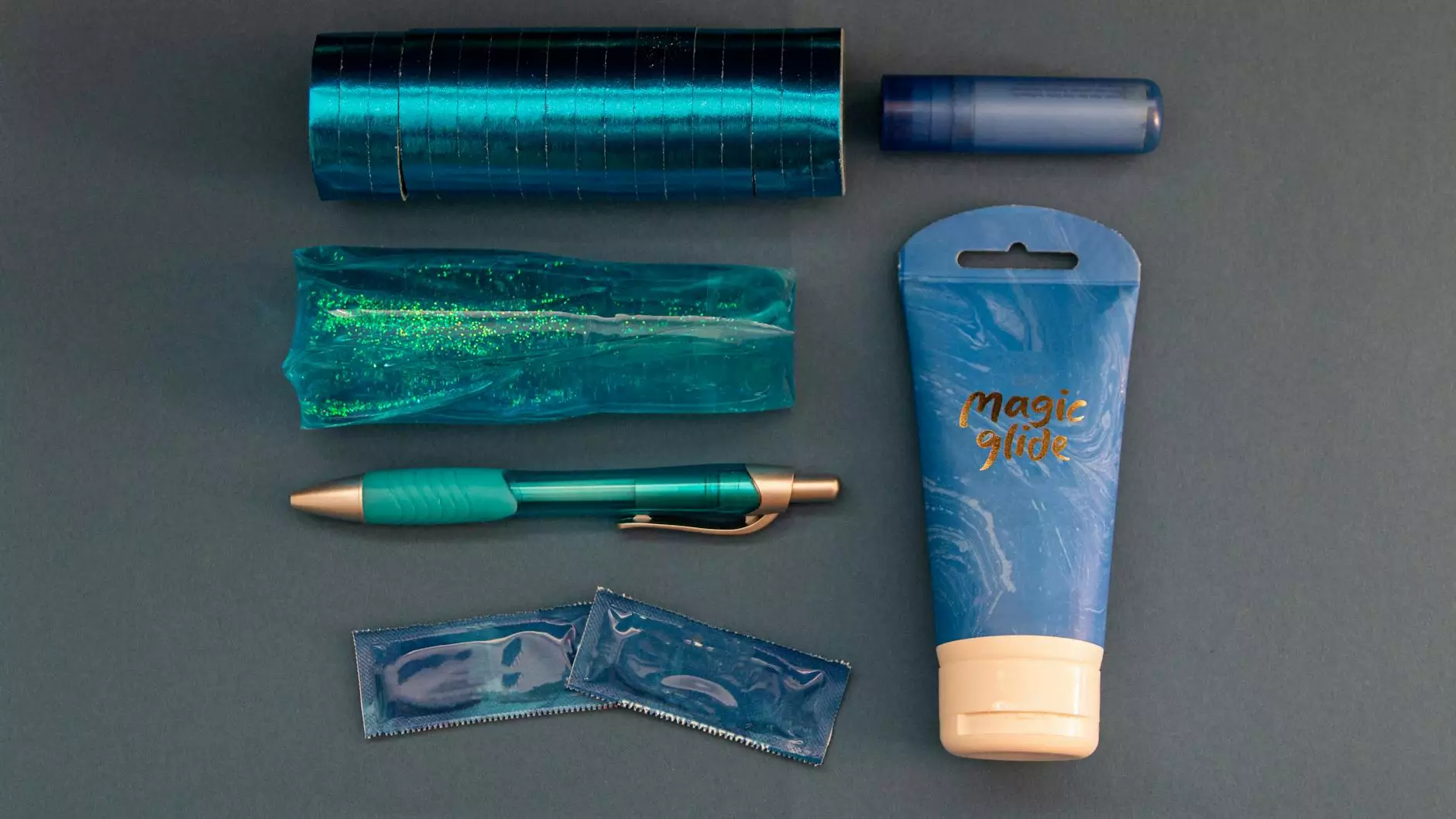
In today's fast-paced and competitive business landscape, operational efficiency and cost-effectiveness are paramount. Companies across various industries are constantly looking for ways to optimize their equipment and processes. One solution that is gaining traction and attention is the implementation of a central lubrication system. This article will delve deep into what a central lubrication system is, its numerous benefits, and why businesses should consider investing in this technology. By the end, you will understand the crucial role this system plays in maintaining and enhancing your operational capabilities.
What is a Central Lubrication System?
A central lubrication system is an automated system designed to supply lubricant to multiple points within machinery and equipment. Unlike traditional lubrication methods, where operators manually grease or oil machines, a central system ensures that every component receives the necessary lubrication consistently. This not only saves time and labor but also enhances the overall performance and lifespan of machinery.
Types of Central Lubrication Systems
Central lubrication systems come in various types, each tailored to different applications and operational needs. Understanding these types helps businesses select the most suitable system for their requirements. Here are the main types:
- Grease Lubrication Systems: Ideal for industries that require a thicker lubricant, grease systems facilitate the consistent application of grease across multiple machine parts.
- Oil Lubrication Systems: These systems are designed for environments where oil is the preferred lubricant. They offer excellent flow and cooling properties, making them suitable for high-speed applications.
- Dual Line Systems: Utilizing two independent lines, this system provides lubrication to multiple points simultaneously, making it efficient for larger machinery setups.
- Progressive Lubrication Systems: Known for their reliability, these systems push lubricant through a series of progressive distributors, ensuring that each point receives the correct amount efficiently.
Key Benefits of Implementing a Central Lubrication System
1. Increased Equipment Efficiency
One of the most significant advantages of installing a central lubrication system is the increase in overall equipment efficiency. With a consistent supply of lubricant, machinery can operate smoothly without interruptions caused by friction or overheating. This improved operational flow leads to enhanced productivity and better output.
2. Reduced Labor Costs
Manual lubrication requires significant labor and time, diverting resources from other critical tasks. A central lubrication system automates the lubrication process, reducing the need for manual intervention. This leads to lower labor costs and allows employees to focus on more value-added activities.
3. Longer Equipment Lifespan
Regular and precise lubrication is vital for maintaining the health of equipment. A central lubrication system ensures that all parts are adequately lubricated, significantly reducing wear and tear. Consequently, the lifespan of machinery extends, resulting in lower replacement costs over time. Investing in a central lubrication system can considerably reduce the total cost of ownership of your assets.
4. Fewer Downtimes
Unexpected machinery failures can lead to costly downtimes. By adopting a central lubrication system, businesses can minimize these occurrences. The system routinely delivers lubrication, preventing parts from seizing or breaking down due to insufficient lubrication. Predictive maintenance can also be integrated, allowing for proactive repairs and replacements.
5. Enhanced Worker Safety
A central lubrication system not only benefits machinery but also improves workplace safety. Manual lubrication can expose workers to hazardous conditions, such as slips from lubricants or working in cramped spaces around machines. With a central system, the necessity for manual lubrication tasks diminishes, creating a safer environment for employees.
Applications of Central Lubrication Systems
Central lubrication systems are versatile and find applications across various industries. Here are some notable examples:
- Manufacturing: In factories, these systems keep heavy machinery running efficiently, thereby maximizing production output.
- Automotive: Central lubrication is crucial in the automotive sector, where it is employed in assembly lines and vehicle maintenance operations.
- Agriculture: Tractors and farm equipment benefit from consistent lubrication, enabling them to operate under heavy loads and diverse environmental conditions.
- Construction: Heavy construction equipment requires regular lubrication to function properly and safely across rugged terrains.
- Mining: Equipment used in mining operations faces extreme conditions, making reliable lubrication systems essential for continuous operation.
How to Choose the Right Central Lubrication System for Your Business
Selecting the right central lubrication system requires careful consideration of various factors. Here are some critical aspects to evaluate:
1. Understand Your Lubrication Needs
Analyze the specific lubrication requirements of your machinery. Different machines may require different types of lubricants, such as oil or grease. Understanding these needs is fundamental to selecting an appropriate system.
2. Evaluate the Size and Complexity of Your Operation
The size of your facility and the complexity of your machinery will play a significant role in the type of central lubrication system you require. Larger operations with multiple machines may need more intricate systems with advanced features.
3. Budget Considerations
While the cost of implementing a central lubrication system can vary, investing in high-quality systems often results in better long-term savings. Be sure to assess both initial costs and potential return on investment (ROI) when making your decision.
4. Consult with Experts
Engaging with lubrication system professionals can provide invaluable insight. Experts can help you analyze your specific requirements and suggest systems that will deliver the best performance and reliability for your operations.
5. Consider Service and Maintenance
Choose a lubrication system that comes with robust support and maintenance options. Regular servicing ensures that the system functions efficiently and remains reliable over time.
The Future of Central Lubrication Systems
The evolution of technology continually shapes the capabilities of central lubrication systems. Innovative developments in automation, monitoring, and control systems are making these solutions even more effective. Features such as IoT integration allow businesses to monitor lubrication levels remotely and optimize maintenance schedules accordingly.
As industries look toward increasingly sustainable practices, central lubrication systems also enhance energy efficiency, minimizing waste and promoting responsible resource use.
Conclusion
For businesses looking to improve operational efficiency, reduce costs, and extend the lifespan of their equipment, investing in a central lubrication system is a smart decision. The advantages are clear: enhanced efficiency, reduced labor, increased safety, and the promise of minimized downtime. By selecting the appropriate system tailored to your needs and consulting industry experts, companies can unlock the full potential of their machinery and maintain a competitive edge.
At fitsch.cn, we offer a variety of high-quality fittings and lubrication systems tailored to meet industry demands. Our commitment to excellence ensures that every solution we provide contributes to your operational success.