Understanding the Dynamics of a Rubber Blades Factory
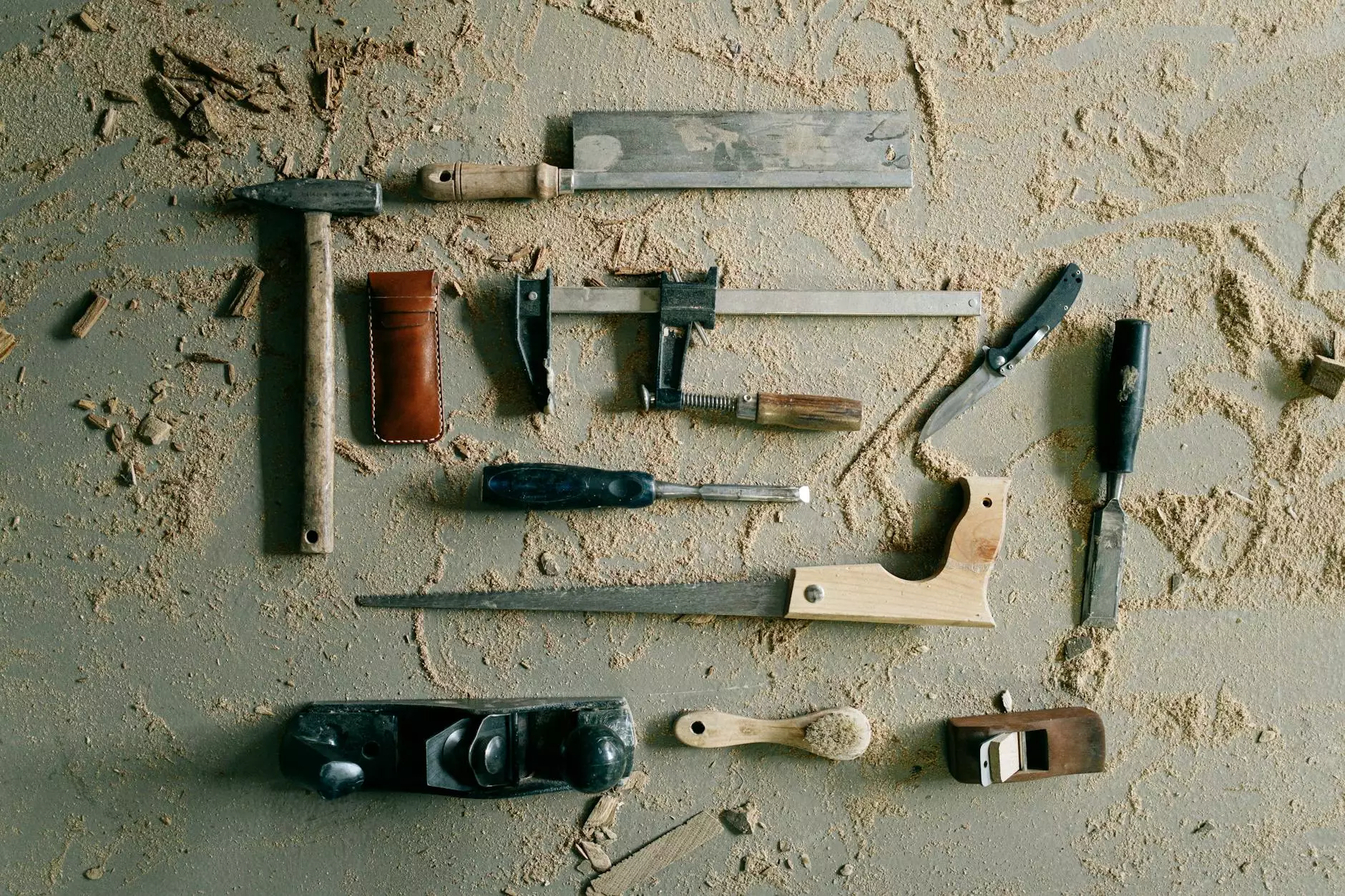
The rubber blades factory is an essential hub for innovation and quality in the manufacturing sector. It is not only about producing rubber blades but also about setting new standards in professional services and knife sharpening techniques. In this comprehensive article, we will explore various aspects of running a successful rubber blades factory, including manufacturing processes, product applications, and the significance of sharpening techniques in production efficiency.
The Importance of a Rubber Blades Factory in Modern Manufacturing
Rubber blades play a crucial role in various industries, making the rubber blades factory a valuable asset in today’s competitive marketplace. The following points highlight the significance of these factories:
- Diverse Applications: Rubber blades are utilized in a myriad of applications including packaging, printing, and industrial machinery.
- Cost Efficiency: High-quality rubber blades contribute to reduced operational costs by improving efficiency and lifespan.
- Innovation: A well-equipped factory is often at the forefront of research and development, creating new blends and designs for better functionality.
- Sustainability: Many rubber blades factories are incorporating eco-friendly practices, reducing waste, and improving production processes.
Manufacturing Processes in a Rubber Blades Factory
Understanding the manufacturing processes is vital to appreciating the complexity of a rubber blades factory. Each step in production can affect the quality of the final product. Here’s an in-depth look at the various stages involved:
1. Raw Material Selection
The foundation of any successful manufacturing process begins with raw materials. In rubber blade production, selecting high-quality rubber compounds is crucial. These compounds are chosen based on their intended application:
- Natural Rubber: Known for its elasticity and tensile strength.
- Synthetic Rubber: Offers superior resistance to aging and weathering.
- Recycled Materials: Emphasizing sustainability and reducing carbon footprint.
2. Mixing and Compounding
Once the raw materials are selected, they are mixed to create a compound that meets specific performance requirements. This process involves:
- Batch Mixing: Combining rubber with additives such as fillers and accelerators.
- Homogenization: Ensuring an even distribution of materials within the compound.
3. Molding and Extrusion
The compounded rubber is then shaped into desired forms through various methods.
- Molding: Using steel molds to create specific shapes and sizes.
- Extrusion: For producing continuous lengths of rubber blades with uniform cross-sections.
4. Curing (Vulcanization)
Vulcanization is a critical process that enhances the chemical and physical properties of rubber. This involves heating the rubber to form cross-links between the rubber molecules, improving the durability and performance of the blades.
5. Finishing Operations
After curing, the blades undergo finishing operations such as trimming, grinding, and surface treatments. These processes ensure that the blades meet the quality standards required for different applications.
The Role of Professional Services in Rubber Blade Manufacturing
Professional services play a pivotal role in enhancing the efficiency and effectiveness of a rubber blades factory. Here are key services that are indispensable:
1. Quality Control and Testing
An established factory implements rigorous quality control measures, including:
- Material Testing: Verifying the integrity and conformity of raw materials.
- Product Testing: Performing tests under operational conditions to ensure performance standards.
- Certification: Acquiring certifications such as ISO to signal quality assurance.
2. Engineered Solutions
Many factories now offer engineered solutions tailored to client specifications, enhancing the value they provide. This may include:
- Custom Designs: Creating rubber blades that are tailored for specific machinery or applications.
- Technical Support: Offering expertise during the procurement and installation phases.
3. Knife Sharpening Services
Knife sharpening is crucial in maximizing the performance and longevity of rubber blades. Factories often provide:
- In-House Sharpening: Maintaining the performance of blades used in manufacturing processes.
- Training for Clients: Educating clients about effective sharpening techniques to improve efficiency.
Emerging Trends in the Rubber Blade Industry
The rubber blades factory industry is evolving with new trends that focus on environmental sustainability, technological advancements, and automation. Key trends include:
1. Sustainability Initiatives
As sustainable practices gain momentum, manufacturers are exploring various avenues, including:
- Recycling Programs: Implementing systems to recycle old rubber blades.
- Green Certifications: Achieving certifications for eco-friendly manufacturing processes.
2. Incorporation of Technology
Digital technologies are reshaping rubber blade manufacturing through:
- Automation: Streamlining production lines to enhance efficiency.
- Data Analytics: Utilizing data to monitor production metrics and improve quality.
3. Enhanced Customization
Advancements in production technologies allow for more customized solutions, leading to:
- Quick Turnaround: Rapid response to market changes through flexible manufacturing.
- Client Collaboration: Working closely with clients to develop specific requirements.
The Future of Rubber Blades Factories
The future of the rubber blades factory market holds promising opportunities. Factors such as growing demand in emerging economies, advancements in manufacturing techniques, and a push towards environmental sustainability will shape this landscape.
1. Market Growth
With industries such as packaging and automotive expanding, the demand for high-quality rubber blades is expected to rise. This offers opportunities for factories to explore international markets and diversify product offerings.
2. Innovation in Materials
The development of new rubber compounds that offer greater durability or incorporate features such as temperature resistance will likely become a focal point of future production.
3. Strengthening Supply Chains
Factories are increasingly focusing on enhancing their supply chains to ensure quick availability of raw materials, which is vital in meeting production demands.
Conclusion
The rubber blades factory serves as a cornerstone in the modern manufacturing arena, offering critical support across various industries. By leveraging professional services, adopting innovative practices, and focusing on sustainability, these factories are poised to thrive in a competitive environment. As we look to the future, it is evident that continuous improvement in manufacturing processes and sharpening techniques will be key drivers of success, ensuring that rubber blades remain indispensable tools in diverse applications.
For businesses seeking to optimize their operations with high-quality rubber blades, working with an experienced manufacturer like szblade.com is paramount. Embrace the future of manufacturing today!